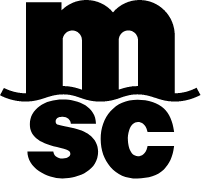
/tr/lp/blog/shipping/seasonal-shipping-supply-chain-shipping
Keeping Supply Chains Strong Amid Global Celebrations: Managing Holiday Peaks
19/12/2024
Whether it’s Chinese New Year, Labour Day, Christmas, Ramadan, or Diwali, globally there are so many exciting celebrations that take place throughout the year.
With these holidays come changes in consumer behaviour, with more people taking time to relax and celebrate. This also brings about changes in consumer demand, due to the amount of pre-planning and potential spending by your customers ahead of the holiday season.
For retailers, preparing for international holidays requires significant preparation to ensure they can deliver the best service for their customers. Not only is demand higher, but the potential for various members of the workforce to be on leave, combined with the risk of weather-related delays or port congestion can lead to significant supply chain disruption if thorough planning is not completed.
Get a quote and ship MSC with the leader in shipping and logistics.
The Domino Effect of
Seasonal Shipping
Seasonal shipping can cause a massive domino effect which can impact your entire logistics strategy if properly not managed.
Any issue in the early stages of your supply chain, like port congestion can result in your cargo being delayed in its journey towards its destination. Not only is this frustrating for customers, but as a retailer, the consequences can be devastating. In a 2021 study by McKinsey & Co., it was found that if a product was out of stock with one company, 70% of shoppers would pick another store or brand. In the short term, having these limited supplies of popular stock could lead to a loss of revenue, while in the long- term this could impact your brand reputation and cause you to lose out to your competitors.
The Domino Effect of
Seasonal Shipping
Seasonal shipping can cause a massive domino effect which can impact your entire logistics strategy if properly not managed.
Any issue in the early stages of your supply chain, like port congestion can result in your cargo being delayed in its journey towards its destination. Not only is this frustrating for customers, but as a retailer, the consequences can be devastating. In a 2021 study by McKinsey & Co., it was found that if a product was out of stock with one company, 70% of shoppers would pick another store or brand. In the short term, having these limited supplies of popular stock could lead to a loss of revenue, while in the long- term this could impact your brand reputation and cause you to lose out to your competitors.
The Domino Effect of
Seasonal Shipping
Seasonal shipping can cause a massive domino effect which can impact your entire logistics strategy if properly not managed.
Any issue in the early stages of your supply chain, like port congestion can result in your cargo being delayed in its journey towards its destination. Not only is this frustrating for customers, but as a retailer, the consequences can be devastating. In a 2021 study by McKinsey & Co., it was found that if a product was out of stock with one company, 70% of shoppers would pick another store or brand. In the short term, having these limited supplies of popular stock could lead to a loss of revenue, while in the long- term this could impact your brand reputation and cause you to lose out to your competitors.
On the other hand, overstocking is not the solution to managing potential disruptions during the holiday season. In 2022, according to McKinsey & Co between 30-50% of retailers had more available stock then they needed. For peak items, this can lead to big discounts to ensure stocks are sold which results in narrower profit margins. Alternatively for items that are less seasonal, this type of over stocking may result in retailers paying higher warehouse fees to store the extra stock.
Although each company may be impacted differently during holidays, there are a few factors that you should be mindful of when considering how to manage seasonal shipping.
Early Shoppers
Everyone knows that when it comes to a big celebration, preparation is key. With that in mind, more and more customers are starting their holiday shopping earlier than ever. This can cause a strain on your inventory levels if unaccounted for, which in turn puts pressure on vendors and other stages in your supply chain to restock your business with high-demand products quickly.
Disruptions to Vendor's Supply Chains
Your business cannot operate in isolation, and therefore you are reliant on your vendors to also maintain good supply chain management in the lead-up and throughout holiday peaks. With more workforce taking annual leave during peak holiday times, factories can close or have limited production lines, which impacts both your vendors and your logistics plans.
As well as preparing to ensure that everything in your supply chain works perfectly, when it comes to seasonal shipping success it’s also important to prepare for things to go wrong.
Plan your Shipments Early
Pre-planning your shipments as early as possible is an invaluable way to avoid global supply chain disruption. Not only does it allow your vendors time to source the products you need well in advance of shipping your cargo, but it also affords your business more time to correct and address any issues or bottlenecks within your operations before the high-pressure seasonal shipping starts.
As a retailer planning and organizing early shipments also allows you to capitalize on the business brought by early seasonal shoppers. This great for your profit margins, but also for establishing your business as a reliable source of this year’s ‘must-have’ holiday products.
Diversify your Supply Chain
Resilience is a crucial part of successfully managing holiday shipping and diversifying your supply chain is a great way to build this. To reduce your reliance on a single source or supplier, ahead of planning your seasonal shipping, it may be worth identifying reliable suppliers in different regions. This prevents your business from being impacted if one supplier has limited production lines for a certain period, or if weather conditions mean that cargo travelling by certain shipping routes will be delayed. This helps reduce your stress levels during the holiday season by making sure you have enough stock on the shelves to meet your customer’s demands.
Leverage Technology
Digitalization and technological developments are beneficial across all stages of your supply chain and can help to make the seasonal shipping process much smoother.
Tools like predictive AI software analysis or freight forecasting can help you analyse historic trends and anticipate fluctuations. This data can be used to help you build contingency plans which ensures that if delays or disruption do occur, your cargo is still able to reach your customers in time for the holidays.
Increase inventory levels
As a retailer, being able to anticipate potential levels of consumer demand ahead of the holiday season provides you with ample opportunity to increase your inventory levels ahead of the holiday season. Increasing your inventory levels for popular products (without overstocking) ahead of the peak in demand reduces the strain across your supply chain that can occur when trying to acquire high levels of cargo quickly.
It's important to not just rely on predictive tools, however. As a business you know your industry and your customers, so increasing inventory levels across as much of all your popular stock as possible is advisable.
Collaborate with Reliable Logistics Partners
Similarly, working with a reliable, experienced logistics partner is a huge advantage when it comes to avoiding operational disruption. Trusted logistics partners often have extensive networks and transportation routes, which offers your supply chain increased flexibility. As a result, in cases where delays may occur, you’ll be able to adjust your supply chain accordingly through your logistics partners.
Equally, experienced logistics partners, like MSC, also have the size to help you scale up your supply chain during peak seasons of shipping. This helps prevent bottlenecks and makes sure that your cargo arrives at its destination on time and in good condition.
Ask MSC
Here at MSC, we provide consultation and advice on all your shipping requirements for the automotive industry, as well as a complete range of shipping and logistics services. Contact us today to find out more.
Discover our Range of Solutions
Warehousing & Storage Solutions
Learn MoreShipping Solutions
Learn MoreInland Transportation & Logistics Solutions
Learn More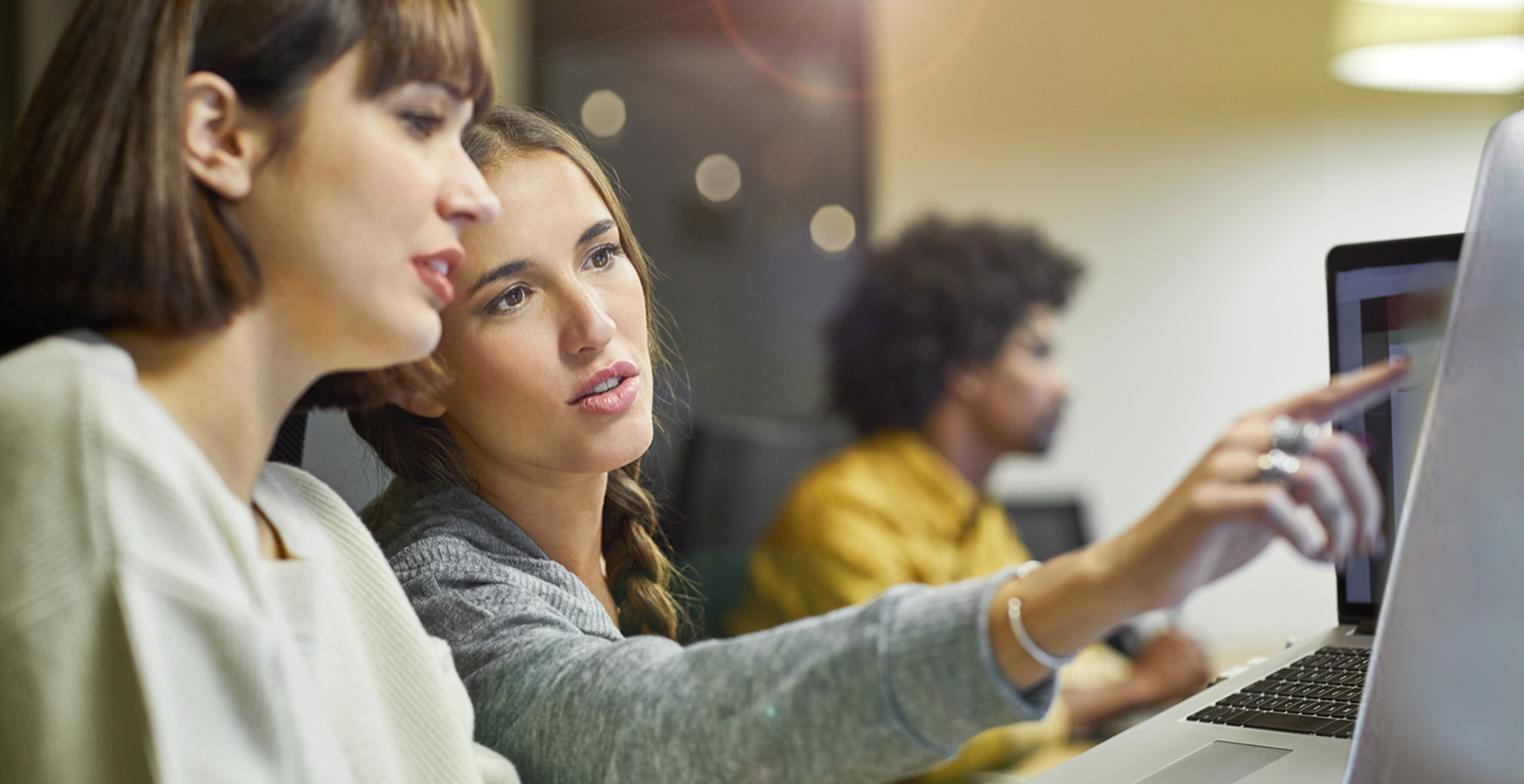
Digital Business Solutions
Learn More